How Encoders Provide Motor Speed and Position Control
In many mechanical systems, precise motion hinges upon effective monitoring and control of the motor. Encoders make motion control possible by sensing the motor’s speed and position and sending feedback signals to control components. Two square waves, or channels, shifted 90 electrical degrees from each other, along with an optional index pulse that occurs once per revolution, encode the angular position data.
Read More
Topics:
Motor Application Tips,
Encoders,
motor performance
Motor Selection Tips: Understanding Thermal Parameters of DC Coreless Motors
With the help of simple thermal modeling
When trying to understand the phenomenon of heating of coreless dc motors, its helpful to express it as a simple thermal model and to draw an analogy with an electrical system. Looking at Fig. 1, you can see the power dissipated (heat) is the difference between electrical input power and the mechanical power (speed & torque) generated by motor shaft. With this basic understanding , let’s next examine the thermal model of a DC coreless motor.
Read More
Topics:
Motor Application Tips,
Brush DC Motors
Why Use an Electromagnetic Brake with Your Electric DC Motor?
Electromagnetic brakes are used in industrial and medical equipment to consistently hold a load in position at a specific stopping point. The brake hollow shaft is mounted on an electric motor shaft for a compact integration.
Read More
Topics:
Others,
Motor Application Tips,
Robotics
Portescap E-Store – Mini Motor Purchasing Available On-Line
Portescap has opened our new E-Store where you can find and purchase miniature motion technologies to suit any configuration, environment, or envelope. All Portescap motor technologies are available for review including Brushless DC, Coreless Brush DC, and Stepper (Can Stack, Disc Magnet, and Linear Actuator). You can view all motors within a technology and drive down to an individual motor page for a deeper evaluation. Once your selection is ready, you can purchase directly in the store if available or submit a request for a quote on the product.
Read More
Topics:
Others,
Motion Compass,
Motor Application Tips
Motor Sterility Management: Protecting vs. Autoclaving
Surgeries must be performed using sterile equipment to prevent infection. While some simple surgical tools can be manufactured inexpensive enough to be economically thrown away after each use, more sophisticated tools such as drills, saws, and shavers must be reusable and therefore sterilized. The motor is a critical part of these tools, and if not protected properly, its electronic components can be susceptible to the moisture and temperature of the steam sterilization process (autoclave).
Read More
Topics:
Medical & Diagnostics,
Others,
Motor Application Tips,
Surgical Motor Solutions
How to Optimize Your Product or Device Output
Early engagement with an Application Engineers (AE) can be a valuable first step when working on your application design and looking for the optimal motion solution. Our AEs will gather valuable information during the motor selection process, to ensure that they use the right motor for the allotted space and application. After a thorough analysis and discussion, they can provide speed/torque curves for various motor options. If they know the duty cycle, they can help to determine whether or not to use a smaller motor in a temporary overdrive application.
Read More
Topics:
Others,
Motor Application Tips
Seeing beyond what's in the catalogue: Why it's important to get in touch with Portescap
Finding the right motor can be a challenge. Often a product catalog only lists a selection of available motors and coils, so the ideal solution can't be found by browsing through available standard options. Some motor manufacturers offer customizations, which require time and money to be invested and might not always be an option depending on the size of the project.
Read More
Topics:
Others,
Custom motors,
Motor Application Tips
Driving DC Brushed Motors
To control a DC motor, a variable, and controlled power supply is needed. There are three types of methods that can be used:
- Voltage-controlled linear supply
- Current linear supply
- PWM (Pulse Width Modulation)
Read More
Topics:
Motor Application Tips,
Brush DC Motors
Encoders provide feedback for accurate control of speed and positioning. The rotor angular position is given through two square waves 90 degrees shifted and an optional index pulse occurring once a revolution. There are multiple technologies to get these results.
Read More
Topics:
Motor Application Tips,
Brush DC Motors,
Encoders
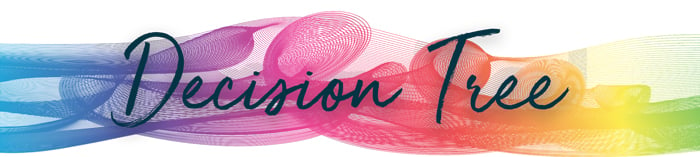
As this series has shown, there are many factors to consider when choosing the optimum motion technology for your application. Your application may have one or more primary factors, which would provide a starting point based on the best technology for that factor or factors. But reviewing all the factors and how they impact the final product output will enable the ideal performance of our product. Below is a summary table for the factors and the three motor technologies:
Read More
Topics:
Motor Application Tips
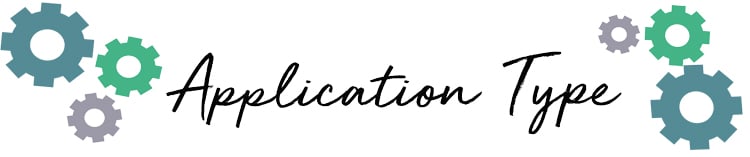
The type of application being designed will dictate different factors be considered for the motion solution. Will the product be stationary? Is the product mobile - being moved by an apparatus or on a person? The typical usage of the product brings forth different factors to prioritize for your motion solution.
Read More
Topics:
Others,
Motor Application Tips
The next factor to review is the duty cycle for the motion solution in the application. The duty cycle is defined as the ratio of the time the motor operates divided by the amount of total time for the cycle. Typically, the motor does not run continuously but rather operates for a period (on-time) and then rests for a period (off-time). The duty cycle affects the selection of the optimum motion solution, so it is important to understand the details and factors to consider.
Read More
Topics:
Others,
Motor Application Tips
Another factor to review is the accuracy required from the motion system in the application. Is the motion continuous or incremental? What is the resolution needed from the motor during incremental operation? Does the motor need to have different resolutions for different points in the operation?
Read More
Topics:
Others,
Motor Application Tips
The next factor for consideration is the mechanical envelope for the motion system. What is the space in the product that is dedicated to the motion system? Is there flexibility on the diameter or length?
Read More
Topics:
Others,
Motor Application Tips
The next factor we will consider is the lifetime requirement of the motion system. How many cycles must the motion system execute within the life of the product? How many hours does that require from the motion system?
Read More
Topics:
Motor Application Tips
The next factor we will consider is the output torque requirement of the motion system. What is the continuous torque requirement during operation? Is there a peak torque for a limited time that needs to be considered? Is the safety margin enough to compensate for the other factors in the application?
Read More
Topics:
Motor Application Tips
One of the first factors to consider in your new product development is the output speed requirement of the motion system. How fast does the motor need to rotate to drive the mechanism in the application? And are there various speeds that need to be accommodated? There are some general guidelines that will help you narrow down the technologies to consider:
Read More
Topics:
Motor Application Tips
What is rotor balancing?
Rotor balancing is the process of bringing the mass center axis of a rotor in line with the rotor’s shaft axis, within certain industry balance standards. A rotor, balanced or unbalanced, wants to revolve around its mass center axis. The balancing process brings these two axes together. As illustrated below, when the mass that causes the imbalance is removed, the two axes merge.
Read More
Topics:
Others,
Motor Application Tips
As a design engineer, there is always excitement when you get to work on new product development. But when you get to the motion portion of the design, there are several technologies to consider, primarily Brushless DC, Coreless DC and Stepper. Which technology is best and where do you start? The challenge can be difficult as there are several factors to consider including output speed, torque, lifetime, mechanical envelope, noise, weight, cost and precision. It is not practical to analyze, purchase and test multiple technologies as this would be expensive and time consuming. Fortunately, there are guidelines that can assist in the initial review of the different technologies to narrow the selection.
Read More
Topics:
Others,
Motor Application Tips,
Quality
In our blog post DC Coreless Speed vs Torque Curves, we talked about how to read speed vs torque curves and the linear relationship of speed and torque for a DC motor. When comparing speed vs torque curves for various motors, the range of torque required in the application should be identified to ensure a proper comparison. The curves will show the torque capability of the motor over the entire speed range, but the application torque range is typically limited to a narrow band.
Read More
Topics:
Others,
Motor Application Tips