Advantages of Gearheads: What to Choose and Why
We know that the purpose of a motor is to provide a certain amount of power to produce a specified amount of speed and torque. In applications requiring a large torque load at slow speeds, it is more economical to use a gear motor (aka gearhead) rather than a large enough motor to provide the specified torque. The gearhead is mounted on the front end of the motor and specific gearing provides the overall speed and output torque. There are various types of gearhead technologies. Here, we will focus on Spur compound and Planetary. Spur gears are designed with the concept of having only one transmission point per train.
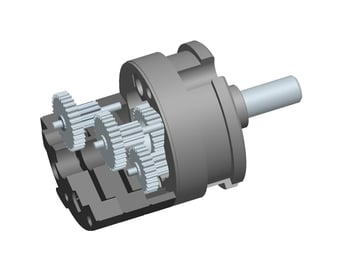
Let’s look at a few benefits of Spur Technology:
- Low friction per train, as single gear mesh in contact
- Multiple trains can be configured to suit design intent
- Input and output shaft not necessarily in line
- Dual output shafts possible
- Direction of rotation can be reversed by using an odd number of reduction stages
Spur Technology provides certain application advantages. It offers very good efficiency - up to 90% to 95% per gear train - including bearing losses. It offers flexible diameter - it can be a long gearhead of small diameter or a short gearhead with a larger diameter. You can choose where to place the motor relative to the output shaft; and it accommodates mounting of a sensor, potentiometer, etc. and offering low noise as compared to a single stage planetary.
Now let's take a look at Planetary Technology. This technology is based on 3 or 4 transmission points per train. More contact points or planets are possible as needed.
The benefits of Planetary Technology are:
- Higher reduction ratio per train is possible compared to spur compound arrangement
- It can provide higher torque
- Input and output of a train have the same direction of rotation
- More rigid construction
There are many application advantages to using planetary gearing. First of all, it offers high efficiency ranging from 85% to 90%, including bearing losses. It offers exceptional performance in a very compact-sized gearhead. You can expect less shock in the case of rapid reversal of motor rotation, and a higher per stage ratio is possible, up to 7:1.
Start by finding the appropriate gearhead that offers the maximum output torque for your application. It is common to see two torque ratings - Static and Dynamic. Static refers to the maximum torque at zero speed and Dynamic refers to the torque rating at speed. Typically, there is a speed/torque curve that will show the capabilities of the gearhead. Consult the gearhead manufacturer to understand the implications higher speed will have on the overall life of the gearhead.
Other meaningful specifications to take note of is radial and axial load specs. This pertains to the recommended specifications on the gearhead shaft in the application. Radial load refers to the force that can be applied to the shaft in the perpendicular direction and axial refers to the force that can be applied in the parallel direction. Axial force is not the same as the parameter for Maximum Press Fit Force which refers to the maximum force that can be used when press fitting a pinion or pully gear onto the motor shaft.
Related spec sheets will provide a mechanical outline and the available ratios for a particular gearhead.
Click here to find the right gearhead for your application.